FIRST | Stronghold
GRT 2015-2016
FIRST Stronghold is played by two alliances of three teams each. Alliances compete against each other to breach their opponents' defenses, known as outer works, and capture their tower. They score points by crossing elements of their opponents' outer works, scoring boulders in their opponents' tower goals, and surrounding and scaling their opponents' tower itself.
Our robot: the Red Giant
For FIRST Stronghold, GRT built the 'Red Giant', a short robot specially engineered to overcome the challenging terrain presented in the game.
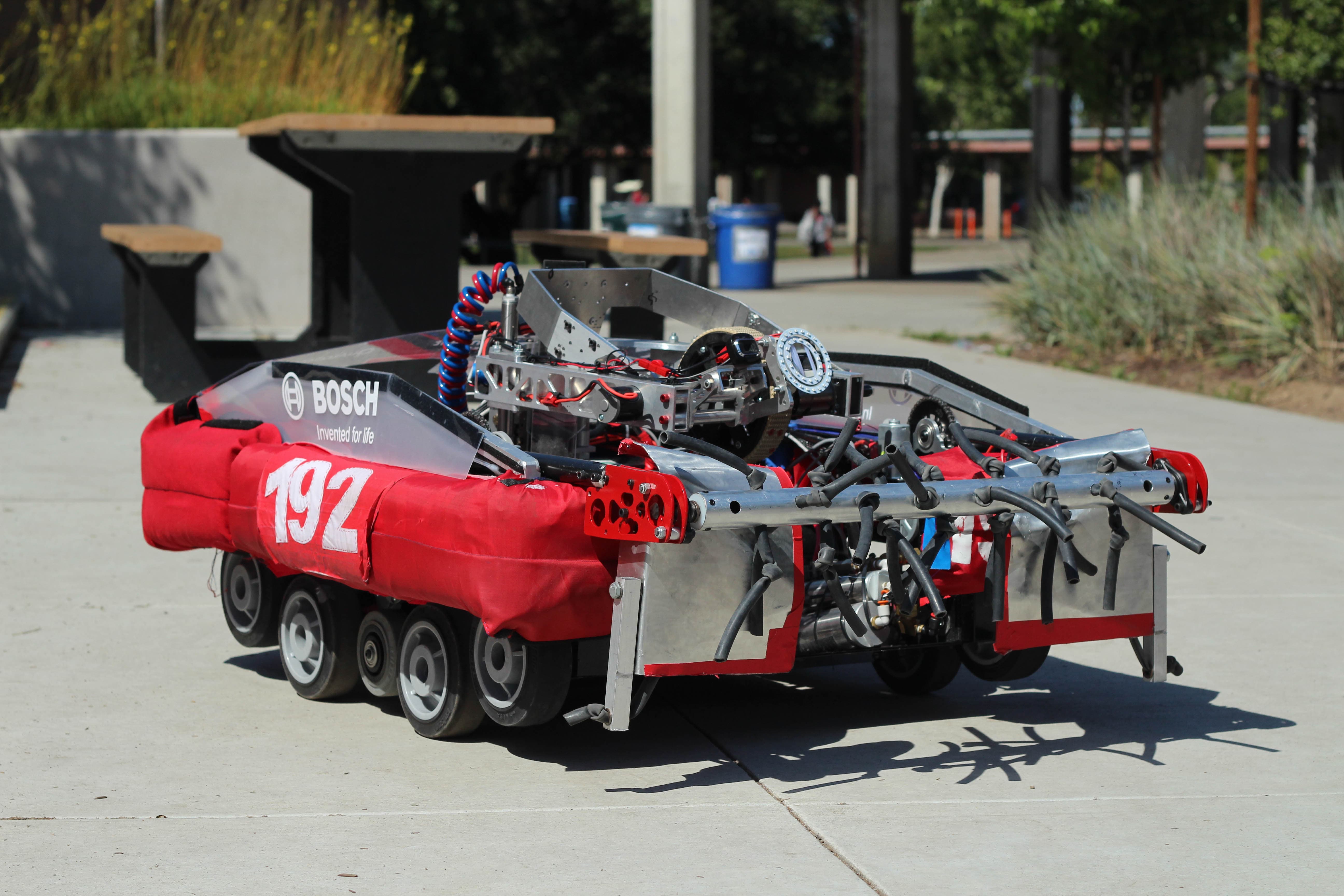
The pickup mechanism on the Red Giant uses two car window motors attached to a roller arm to move the ball into the shooter mechanism. The roller arm consists of a metal roller to which was tied surgical tubing (called 'Chalupa') that served to slap the ball into the robot. The arm was built to cross defenses: wheels were added to the roller arm to move the portcullis up and over the robot, while the entire roller arm is capable of moving up and down in order to cross the Cheval de Frise.
Shooter
For Stronghold, GRT's shooter mechanism was unique compared those on other robots as it contained an integrated shooter and hopper. The flywheel is mounted on top of four pneumatics that raise and lower to create a cage while the ball is in transit, and launches the ball once aimed. When the ball is picked up, the flywheel mechanism is raised so the pickup can deposit the ball in the middle of the shooter. The stationary flywheel is then lowered onto the ball to secure it as the robot drives over the defenses. As the vision tracking software aims the ball at the goal, the flywheel is raised and accelerates up to appropriate speed. The pneumatics then drop the flywheel down onto the ball, launching the ball at the goal.
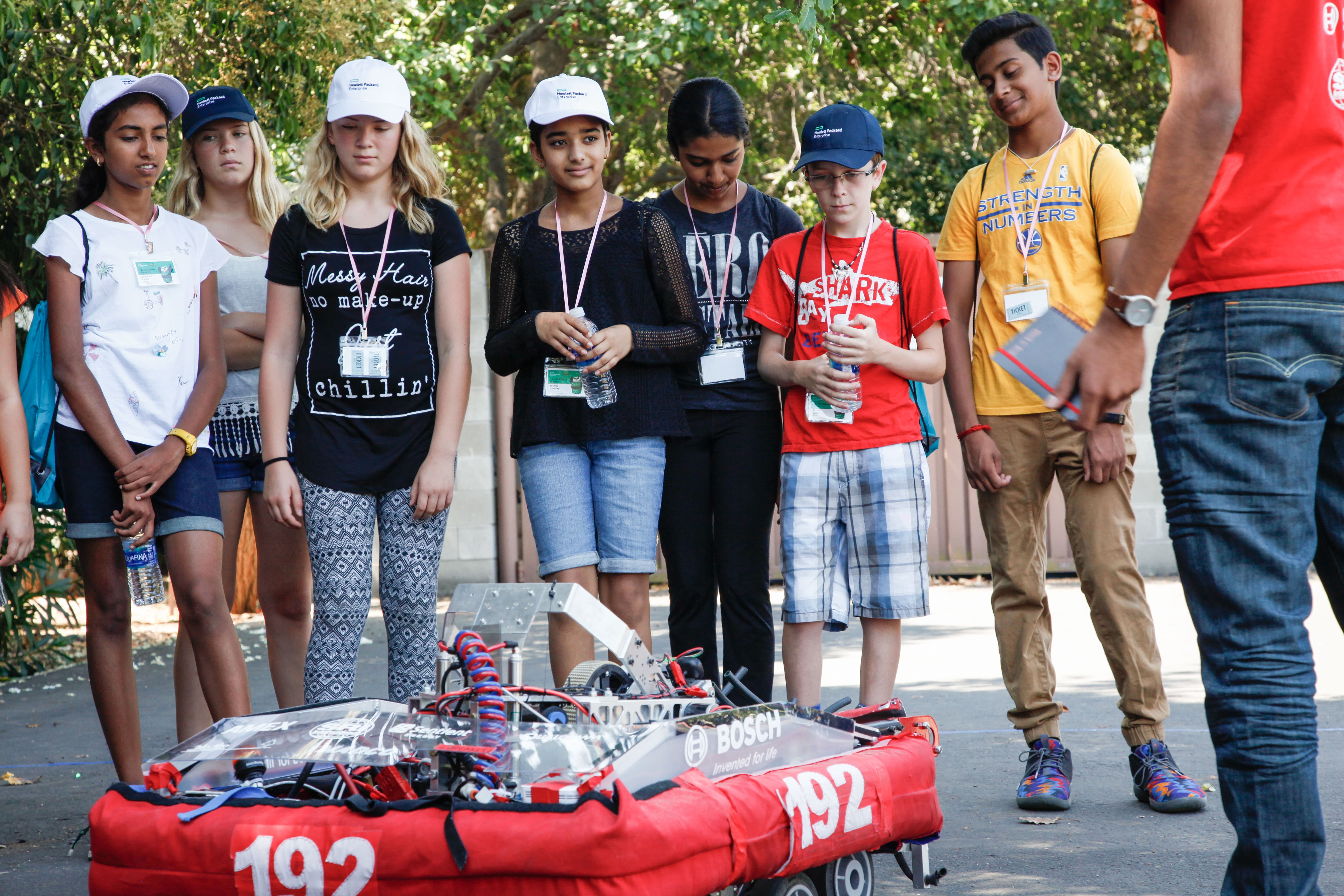
The Red Giant on display.
The shooting mechanism is supported by several aluminum plates and incorporates an adjustable hood to fine tune the arc of the ball upon initial launch. The entire mechanism is set on top of a Lazy Susan that is attached to a motor, which allows the shooter a fairly wide range to aim and shoot.
Drivetrain
This year, our drivetrain team designed a 2-speed gearbox that performed well during competition season. This gearbox consists of 3 CIM motors that use a 3 stage reduction between the motors and the output shaft. The shifting mechanism incorporates a ball shifter that is pneumatically actuated. The shifter uses two pneumatic pistons instead of one to allow the mechanism to shift efficiently with reduced risk of the gearbox seizing during shifting. The high gear was utilized for general movement around the field with a speed of 13.5 feet/second, while the low gear was geared towards aiding the robot claw through defenses better and push other robots if needed (at 6.0 feet/second).
This gearbox was engineered to create space for the robot's other mechanisms. For the past five years, GRT has made an effort to downsize the drivetrain while maintaining and maximizing power output. This has prepared us for the year's game, since many aspects of FRC Stronghold emphasize compactness of design.
Space restrictions
One of the defenses was the low bar, which is about 16" off the ground on an elevated platform. We designed the robot to tackle the low bar from the start. This meant that our robot needed to be designed as small as possible. After creating the initial design for the robot, we examined changes that could be made to the robot's design to create a wider range for the shooter to rotate. This made it easier to aim the shooter when shooting the ball.
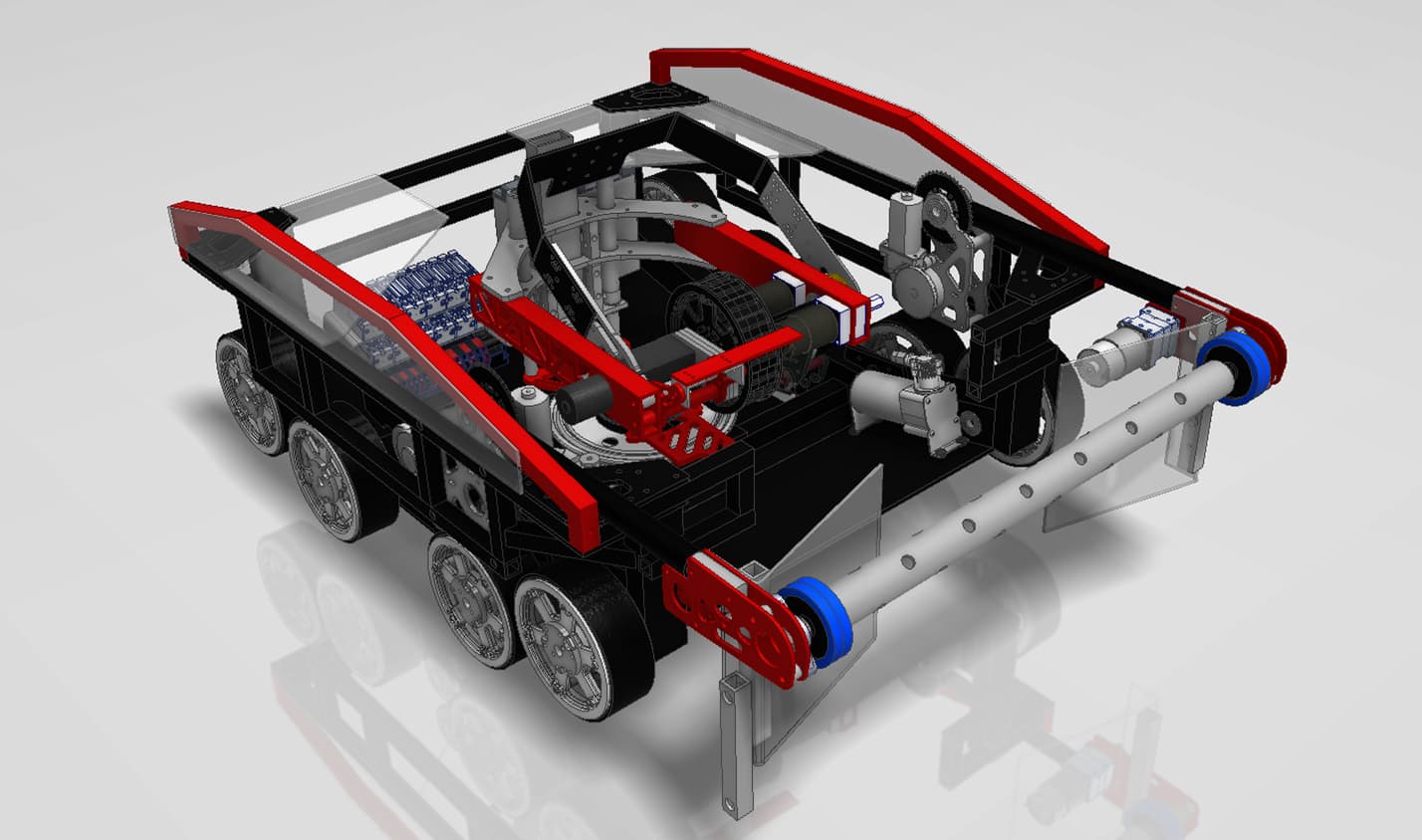
A render of the robot CAD.
Another way we tackled space restrictions was to integrate multiple uses for the same mechanism. For example, the pickup mechanism was utilized for picking up balls and for crossing over two defenses, while the shooter mechanism doubled as a way to store the ball while crossing the defenses. Overcoming the space restrictions allowed us to build a better robot and compete better in competition.
Controls
This year, controls worked hard to give the 'Red Giant' the ability to 'see' the goal. The goals in the towers were surrounded by reflective tape, giving the Controls team the opportunity to use vision tracking software to create a program that could aim the shooter mechanism at the tower, predict the amount of power necessary to make the shot, and adjust the angle of the hood. This software took data from a webcam mounted on the robot that is surrounded by a ring of LED lights. The light emitted from the LEDs is reflected by the tape and received by a sensor. The vision tracking software reads the signals from the sensors and collects data based on this, and subsequently uses an algorithm to obtain the optimal speed of the flywheel and angle of the shooter hood. This setup worked very well during competition and allowed the Controls team to earn the 'Innovation in Control Award' at the Wisconsin Regional.
The team
The 2016 Build and Competition season has been one of our best, from Kickoff Day to our last day at the Silicon Valley Regional (SVR). Our robot performed phenomenally during most of the matches at the regionals that we attended. We were able to become finalists at the Arizona North Regional and advance to the quarterfinals at the other regionals attended. In order to achieve this, GRT worked diligently throughout build season to engineer and fabricate a robot that ended up doing well during competition.