Drivetrain
Drive trains are the systems that make the robot move, and often form the backbone of the chassis. The GRT drivetrain group is well-known within the FIRST Robotics community for our student-designed and -built gearboxes, intricate design work, and precision manufacturing. Since the need for robot movement is universal to any game design, the drive train group does significant work each fall semester to study gearbox designs, practice designing modified versions of past gearboxes, and develop precision machining skills. Redesign considerations range from power use to manufacturability. New designs are fabricated by student machinists in our shop, who create high precision parts on our mills and lathes. One of DT's most important recent achievements is the implementation of "swerve" drive.
Swerve drive allows a robot to be omnidirectional: it can move from side to side without changing the way the robot faces. Other omnidirectional drivetrains such as Mecanum often sacrifice grip to make this happen, but swerve drive maintains traction by using a normal wheel housed in a rotating fork. GRT first started using swerve drive in the 2017 FIRST game, Steamworks, becoming one of the first teams to pioneer the then new drive system. Though swerve has now entered the mainstream, with several manufacturers selling prefabbed modules to teams wanting to try out the unique drive, GRT continues to design and manufacture our own custom swerve, improving and iterating upon previous designs.
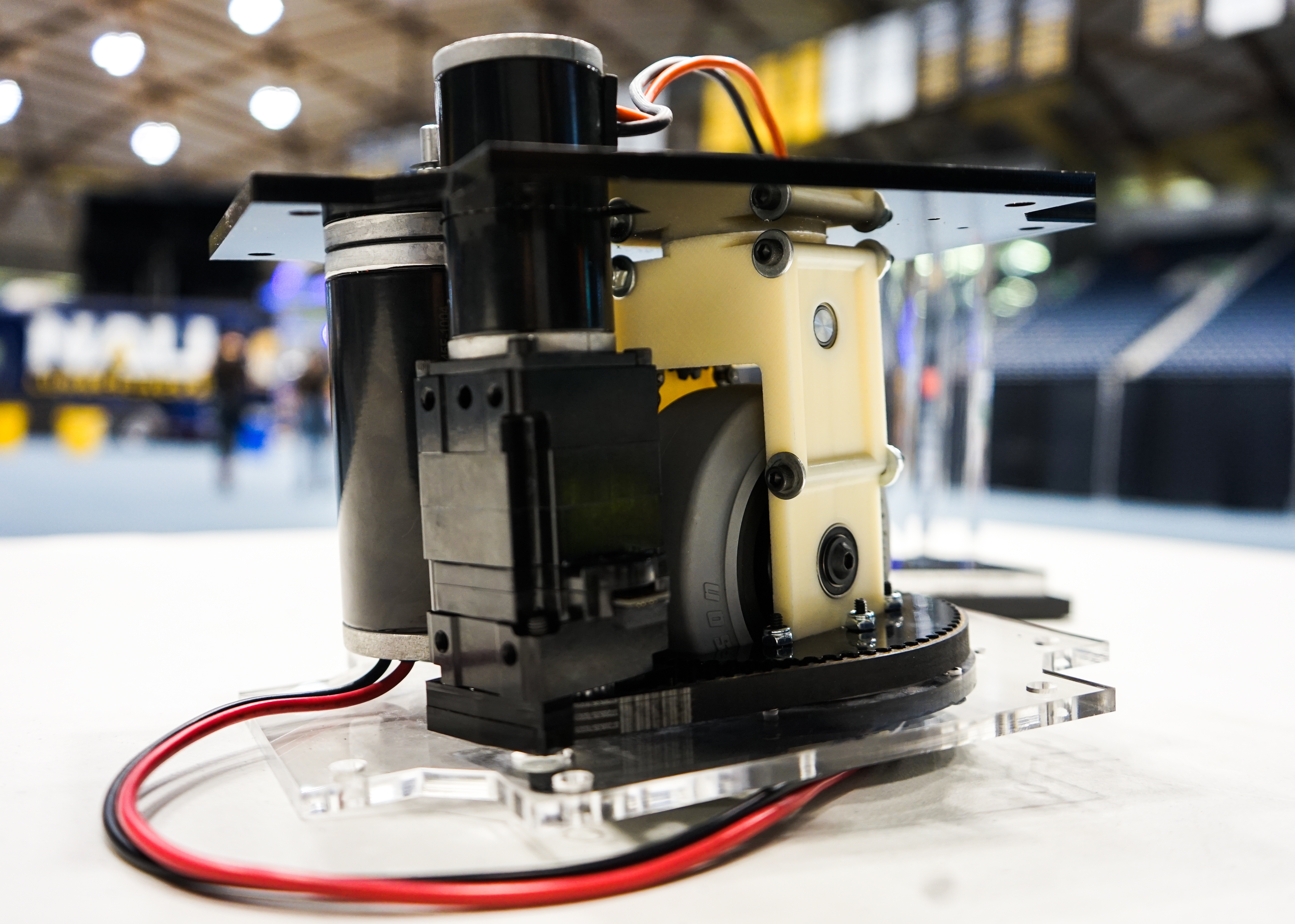
GRT's original 2017 swerve module design.
Historically, GRT has manufactured our own gearbox modules using a variety of machines. For our 2019 gearbox, we used a laser cutter to make custom gears and pulleys, a CNC mill to make gearbox plates, a 3D printer to make swerve gearbox forks, and a lathe to turn all the axles and modify sprockets.
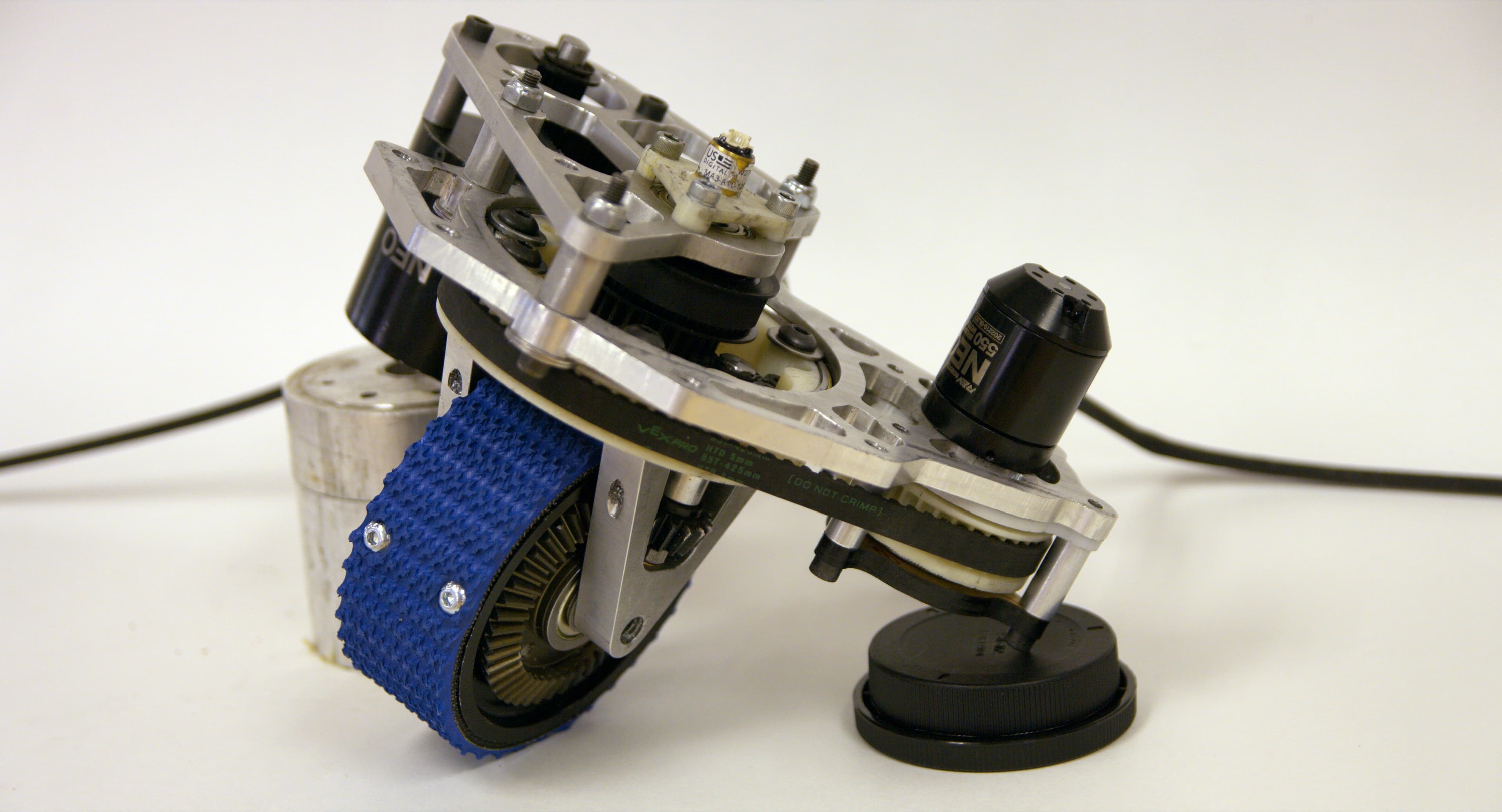
GRT's 2023 swerve module design.
Earlier GRT drivetrains featured 2-speed, ball-shifting gearboxes. Pictured is a shifting gearbox with a 3-stage reduction, which allows the use of 6 inch or larger wheels (a larger wheel would otherwise gear up the transmission).

2016 2-speed gearbox design.
GRT's shifter gearboxes were designed to minimize space requirement, with a footprint extending from the transmissions only 2.7 inches. This came courtesy of several innovations, most notable of which are the inverted shifters: pneumatics that drive the shifting cluster that were turned around and set within the gearbox itself, cutting about 2 inches out of the width. Using this linkage to pull the shifter from afar, the cluster performed better than an off-the-shelf equivalent, holding a gear and shifting down to 25 PSI of pressure. Other innovations include the first reduction of the gearbox, accomplished through a belt drive on the face of the box. This further reduces profile, and allows the motors to be turned backwards, with most of their volume outside of the robot base area.
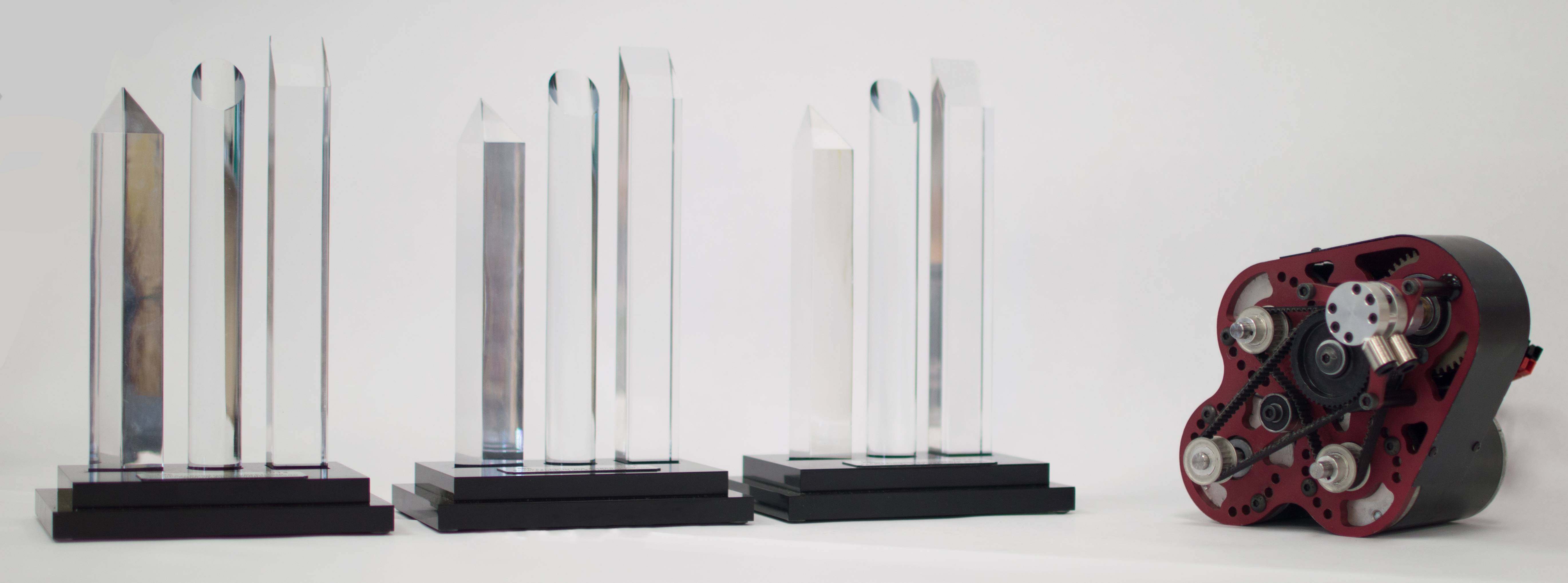
The 2014 shifter gearbox, accompanied by GRT's 3 engineering excellence awards that year.
In tandem with 2-speed drive gearboxes, GRT has used transmissions that transfer power to the wheels via a series of GT3 belts, laid inside box-beam transmission tubes. These box-beam tubes serve as effective housing and as core components of the robot's structure. In response to the terrain obstacles of FIRST Stronghold (2016), GRT adapted this arrangement in a bent-tube design, maintaining the characteristics of our traditional design, while lifting the large front and back wheels off the ground to help us tackle the worst of the obstacles.